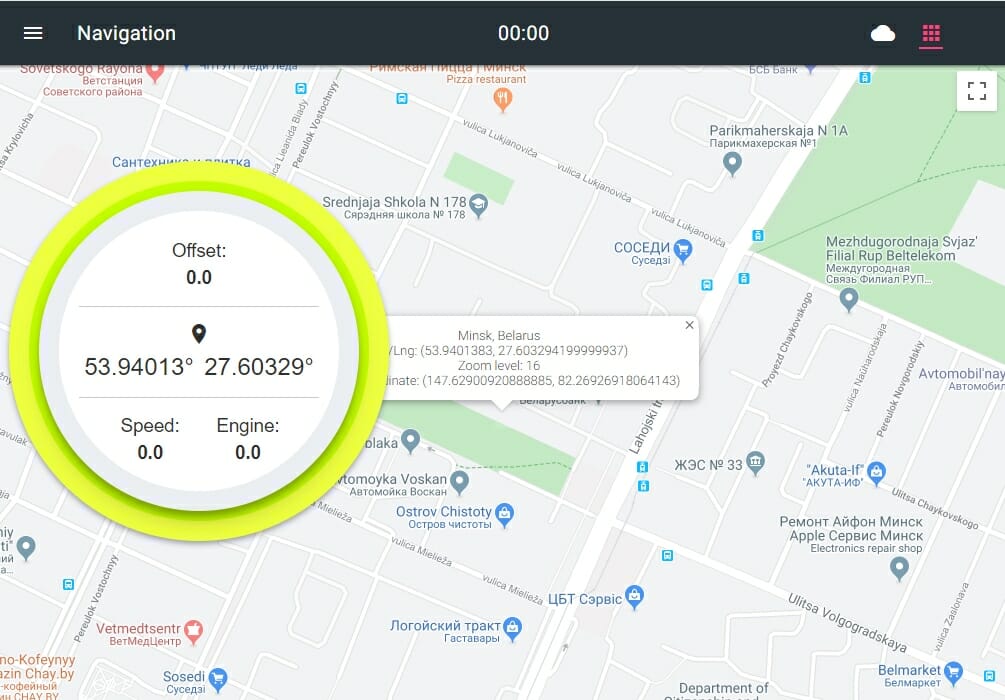
Result Achieved
- Our system can analyze the conformation of the field, plan a trajectory, and drive the tractor at any time and in any weather condition.
- The calculation of the trajectory is very precise and has a margin of error of only 2-4 cm based on the vehicle speed.
- Such technology can reduce cultivation costs per hectare by around $ 60-70 per season. For example, profit will be up to 140 EURO/hectare per year for locations that have two agricultural seasons.
- It is profitable even considering the presence of a worker with simple control tasks inside the vehicle.
Savings in detail
If implemented globally in Belarus, which has one agricultural season, this system could contribute to a cost reduction of approximately $ 250 million dollars per year.
For the European Union, such profit may exceed 7.5 billion EURO annually.
Here are some percentages in detail:
- Fuel and lubes saving up to 30%
- Seeds saving up to 25%
- Fertilizer saving up to 30%
- Plant Protection Savings up to 5%
- Labor cost reduction up to 5%
- Yield increase up to 10%
Key technologies
- C/C++
- Java/JNI
- Kotlin
- GIS/RTKLib
- Python
- TensorFlow/TensorFlow Lite
- Node.JS/WS
- SQL/SQLite
- Android
Introduction
Belarus, the country in which Apro is based, can boast AT LEAST two qualities: great developers and excellent potato farmers. Yep, we could say that potatoes are something like a national symbol.
To honor both of these brilliant aspects of local society, we carried out an R&D project about a self-driving system… for tractors!
The project was developed in partnership with a Russian tech company, where Apro was responsible for the algorithmic and software part.
The goal of our project
Autonomous driving technology is not something new, even in agriculture. In fact, it is commonly used to reduce labor costs and increase driving precision.
However, our goal was to create a universal and sufficiently inexpensive system that could be implemented even by small businesses.
How it works
The system has a unique algorithm that collects data from several sources, combines and processes them in quasi-real-time, making decisions on the fly.
Telemetry detected from each machine is transferred to a special cloud-based system, that is able to store, analyze, and visualize the data.
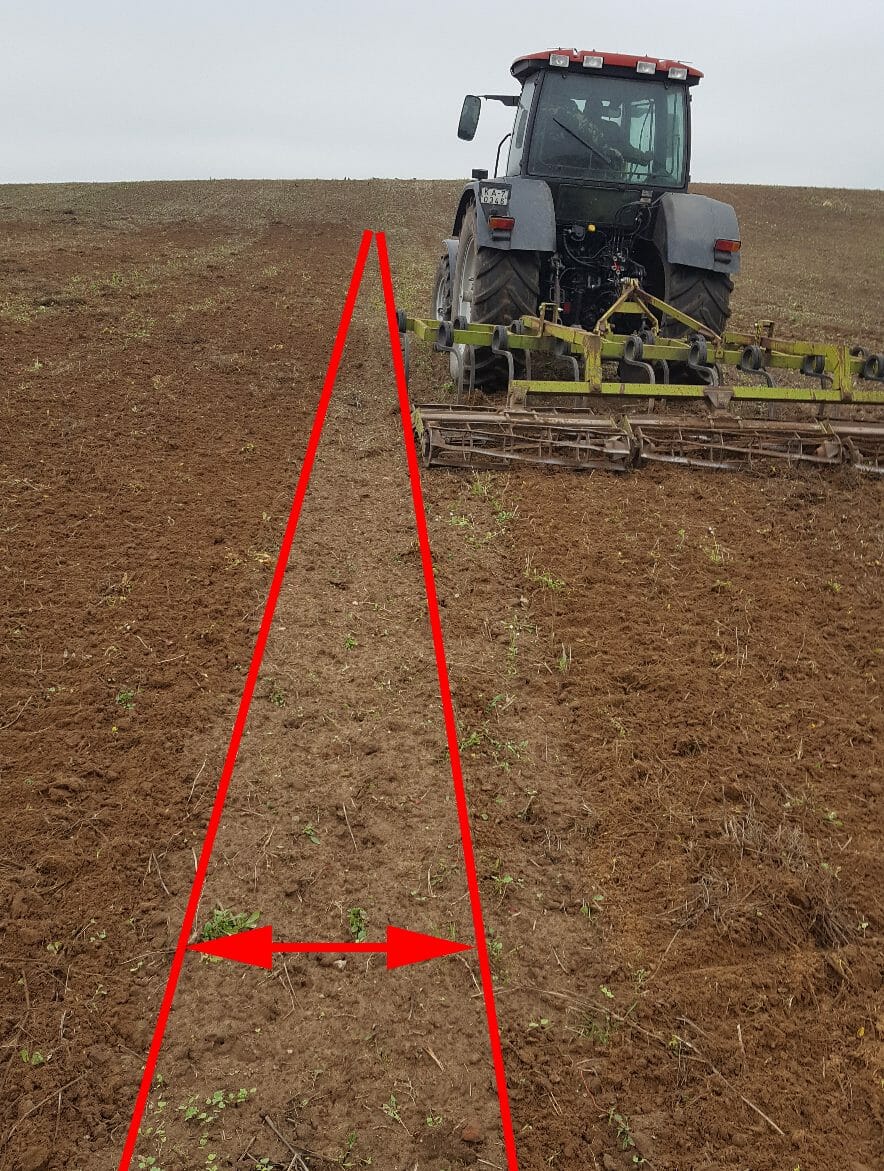
Main issues solved
The system is based on GPS technology but with some corrections. GPS has a margin of error of around 20 meters. Such accuracy is not sufficient for autonomous driving.
We can increase it by installing a portative GNSS base station nearby, which will suggest the appropriate corrections to the machine. This is a fairly common solution in many countries that use similar technologies.
Another problem concerns the positioning of the antenna, which communicates the exact location of the vehicle. It can move slightly and tilt, increasing the margin of error.
For this reason, our system also includes a sensor connected to the antenna and capable of detecting any changes in its inclination.
Safety
- The system is able to lower speed and even stop the vehicle.
- Speed is limited at 20 km/h.
- In case of emergency, the system can switch off the engine.
- The system has visual and audio notifications for the driver.
- 4 ultrasonic sensors are used to detect obstacles on the way. In the event of an obstacle, the system slows down and can stop the vehicle.
Features
- Deep GNSS data processing
- Our own algorithm for matching data from different sources.
- The system uses a limited range of cheap sensors.
- The system can be considered as a base platform without limits on adding new features and 3d-party integrations.
- The system can be installed almost on each agricultural vehicle.